Airbus y Materialise fabrican el primer componente final a la vista con impresión 3D
- Apro Forest
- 11 abr 2018
- 3 Min. de lectura
Cuando se trata de la impresión 3D en la industria aeroespacial, pocas empresas se toman la tecnología más en serio que Airbus.
La compañía se adelantó en la incorporación de la tecnología de impresión 3D en sus aviones; ya en 2015 había colocado más de 1.000 piezas impresas en 3D en su avión A350 XWB, y el año pasado introdujo su primer componente hidráulico de control de vuelo primario impreso en 3D.
Hace un tiempo, Airbus incluso presentó una patente para un proceso de impresión 3D que podía imprimir ”aviones enteros”.

Pieza fabricada con impresión 3D por Materialise 3D.
La primera pieza con impresión 3D a la vista
Más de 1.000 piezas impresas en 3D del modelo de avión A350 XWB están ocultas para los pasajeros, al igual que todas las piezas impresas en 3D de los demás aviones de la compañía.
Sólo ahora, Airbus presenta el primer componente impreso en 3D visible para los pasajeros: un panel espaciador instalado en un avión Airbus A320 operado por Finnair.
Cambio de inyección a impresión 3D
Cuando una aerolínea actualiza el diseño de su cabina, a menudo se crean espacios entre los componentes nuevos y los existentes. Cuando eso sucede, la aerolínea necesita agregar paneles que llenen esos vacíos.
Tradicionalmente, estas piezas de plástico se fabricaban mediante moldeo por inyección, pero se trata de un proceso complejo, especialmente debido a la naturaleza especializada de muchos de los componentes y al número limitado de piezas necesarias para una modernización típica de la cabina. Se necesita un tiempo valioso para que la aerolínea prefiera ser utilizada para recaudar ingresos llevando pasajeros en el aire.

Pieza fabricada con impresión 3D por Materialise 3D (Distanciador).
El uso de la impresión 3D permite hacer pequeños lotes de piezas de forma más fácil y rápida, y también menos costosa.
Las piezas son tan resistentes como las fabricadas con los métodos tradicionales de moldeo, y también se pueden hacer más ligeras, lo que es valioso para los aviones que confían en ser tan ligeras como sea posible para ahorrar costes.
Más modelos fabricados con impresión 3D
Los paneles distanciadores no son los primeros componentes impresos en 3D que pueden ver los pasajeros de los aviones, pero son los primeros para Airbus.
Hasta ahora, ninguno de los componentes impresos en 3D de los aviones había sido considerado lo suficientemente agradable como para ser visto por los pasajeros.
Los paneles fueron impresos en 3D por Materialise, que ha impreso en 3D muchos de los componentes de Airbus, y se están utilizando para rellenar los huecos finales de una fila de compartimentos superiores de almacenamiento.
“Podemos manejar unos plazos de entrega increíblemente ajustados, pero la base para ello reside en un sistema de gestión de calidad cuidadosamente perfeccionado”, dijo el Director de Calidad de Materialise, Geert Appeltans.
“Los paneles espaciadores producidos para Airbus son más que impresiones en 3D, son el resultado de todo un sistema de calidad.”
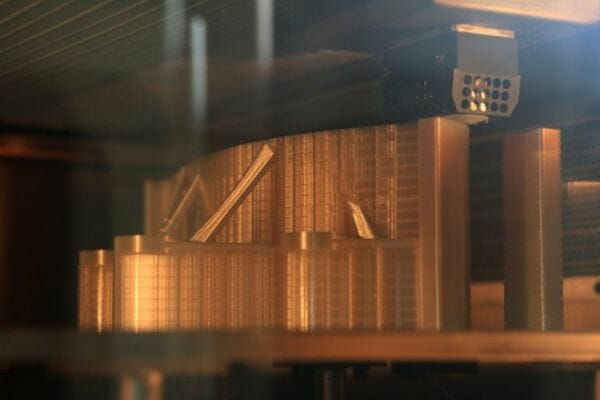
Proceso de impresión 3D con filamento (FDM).
Ventajas de la impresión 3D
El uso de la impresión en 3D permitió a Airbus y Materialise crear paneles bioinspirados que son un 15% más ligeros de lo que habrían sido si se hubieran fabricado utilizando métodos de producción tradicionales.
La impresión 3D también permitió la creación de estructuras de soporte internas complejas, como celosías dentro de los paneles, sin incurrir en costes de producción adicionales.
Los paneles impresos en 3D se pintaron con la pintura ignífuga de Airbus y, a continuación, superaron con éxito todos los controles de acabado y acabado de cabina de Airbus.
Los paneles no son llamativos o ni siquiera tan llamativos; de hecho, la mayoría de los pasajeros probablemente no tendrán idea de que están viendo componentes impresos en 3D.
Los componentes impresos en 3D pueden ahora integrarse de forma tan suave en un entorno de cabina que no sobresalen. Estos pueden ser los primeros componentes de cabina impresos en 3D visibles para los pasajeros, pero es casi seguro que no serán los últimos.
Comentários