CRP Group amplía materiales de impresión 3D SLS
- Apro Forest
- 12 jul 2018
- 4 Min. de lectura
CRP Group, un grupo industrial italiano que integra procesos de fabricación aditiva, como impresión 3D y materiales renovadores de cara al desarrollo de productos, ha ampliado su línea de materiales compuestos Windform para aplicaciones en sectores avanzados como el aeroespacial, automoción, deportes de motor, y sistemas de aeronaves no tripuladas (UAS).
Ofertando una amplia gama de materiales reforzados con fibra de vidrio y carbono a base de poliamida para la impresión 3D SLS, la familia Windform satisface las demandas de los clientes del servicio que requieren componentes de altas prestaciones para pequeñas producciones y piezas de preserie, así como prototipos funcionales.

Prototipo funcional del colector de admisión de automóviles fabricado con impresión 3D en material Windform SP.
Materiales avanzados para impresión 3D
La gama de materiales de impresión 3D funcionales ofrece características deseables como resistencia, rigidez y un acabado superficial atractivo. Materiales como el Windform LX 3.0 se han utilizado anteriormente para crear un portafusibles de motor, prototipos de salpicadero y un asiento de motocicleta para la primera moto eléctrica homologada para circular en Italia: la Energica Ego.
Energica, la filial sostenible del Grupo CRP y primer fabricante italiano de motocicletas eléctricas de altas prestaciones, asimismo ha sido elegida por Dorna como único fabricante para la FIM Enel MotoE World Cup que comenzará en 2019.
La tecnología del Conjunto CRP está apoyando el desarrollo de la bici de carreras totalmente eléctrica Ego Corsa, que va a ser empleada por los equipos que competirán en la FIM Enel MotoE™ World Cup.
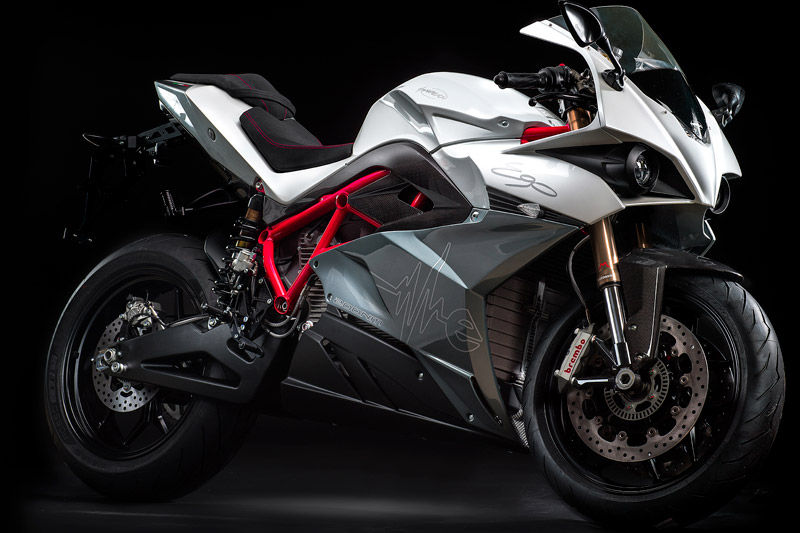
Motocicleta eléctrica Ego Enérgica.
Avanzando en el sector de la fabricación aditiva
CRP Technology, una empresa especializada de CRP Group, se introdujo en el mercado de la fabricación de aditivos en Europa y ahora es uno de los mayores proveedores italianos de soluciones de impresión 3D y prototipado veloz. A resultas de la continua I+D en materiales compuestos, CRP Technology se ha transformado en el fabricante, desarrollador y distribuidor de materiales compuestos Windform para la Unión Europea y el resto del planeta.
De manera comparativa, CRP USA, el socio de fabricación de CRP Group con sede en Carolina del Norte, emplea la línea de productos Windform para crear componentes y prototipos para túneles de viento y de vehículos al servicio de industrias competitivas como la aeroespacial y el automovilismo.

Energica Eva, frontal de la motocicleta eléctrica 3D impreso en 3D acabado y empleado para la serie de pre-producción – material Windform XT 20.
Drone teledirigido Windform impreso en 3D, Tundra-M
Al paso que los materiales compuestos Windform se crearon originalmente para la industria del automovilismo, los clientes del servicio de CRP Technology están aplicando ahora los materiales compuestos en el campo UAS.
Usando materiales de impresión 3D compuestos reforzados con fibra de carbono Windform XT 2.0 y Windform SP, así como la tecnología de impresión 3D SLS, CRP Technology fabricó un prototipo funcional del drone teledirigido Tundra-M.
A través de la integración de los materiales compuestos de Windform y la tecnología de sinterización láser, Hexadrone, una compañía francesa experta en aeroplanos teledirigidos de grado civil y militar, aceleró la fase de desarrollo del producto para los prototipos Tundra-M.
“La tecnología de sinterización láser selectiva Windform nos ha tolerado crear fácilmente prototipos de componentes clave de nuestro producto, superar el proceso de moldeo por inyección de plástico en concepto de plazos, costos y probar nuestro prototipo en condiciones reales con casi exactamente las mismas características mecánicas”, ha declarado Alexandre Labesse, CEO y creador de Hexadrone.
El Tundra-M es el primer avión teledirigido 100% personalizable para usuarios de defensa y rescate.
El Streamliner de NACA
Además, CRP USA fabricó un ducto funcional del National Advisory Committee for Aeronautics (NACA) para el vehículo de carreras Streamliner. El coche del equipo Streamliner de Victory Motorsport batió un récord de velocidad de muchos años en Bonneville Speed Week, un acontecimiento de deportes de motor probando automóviles terrestres adaptados.
Aprovechando la dureza de Windform SP, el ducto NACA fue desarrollado con una elevación exterior alrededor del perímetro del ducto y un “bump” interno. Esto ayudó a dirigir el flujo de aire y reducir la turbulencia del vehículo Streamliner, lo que quería decir que podía operar más eficazmente a grandes velocidades.
“El diseño tiene un poco de dificultad extra para asistir a que el aire fluya en la base de la entrada del Turbo, y parecía un tanto desmoralizador. Debimos construirlo en tres secciones, pero nuestro equipo de acabado fue capaz de aplicar sus conocimientos y habilidades para dar un pulido experto”, dijo Stewart Davis, Directivo de Operaciones de CRP USA.

Conducto NACA puesto en el motor Streamliner. Foto del equipo Victory Motorsport.
El primer satélite completamente impreso en 3D
Los materiales eólicos también están encontrando aplicaciones aeroespaciales a través de la creación del satélite Tubesat-POD (TuPOD). La misión marca un nuevo eslabón en eñ pequeño campo de los satélites, puesto que es el “primer satélite impreso en 3D” que se lanza desde la Estación Espacial Internacional (ISS).
El satélite TuPOD empleó Windform XT 2.0 para su estructura y fue producido en cooperación con CRP USA, Teton Aerospace (Tetonsys), Morehead State University y Japan Aerospace Exploration Agency (JAXA).
Según CRP Technology, el creador de los materiales compuestos Windform, Windform XT, la primera versión de Windform XT 2.0, fue el primer material compuesto relleno con fibra de carbono.
De acuerdo con Amin Djamshidpour, diseñador de TuPOD y cofundador de Tetonsys:
“Utilizando Windform XT 2.0, un material eléctricamente conductor y mecanizable en la fabricación 3D de TuPOD fue una de las mejores decisiones que hemos tomado. Durante la fase de prototipado e incluso durante la fabricación final, nos encontramos con múltiples situaciones en las que necesitábamos taladrar la pieza o realizar pequeñas modificaciones en la estructura impresa en 3D y trabajar con Windform XT 2.0 nos dio la capacidad de hacerlo”.
CRP también utilizó este material para imprimir piezas en 3D para el KySat-2 CubeSat en 2013.

Despliegue del TuPOD. Foto vía JAXA/NASA.
La tecnología compuesta Windform Laser Sintering, probada en desgasificación, personalizable, aprobada para contacto con la piel y aplicable a complejos componentes estructurales impresos en 3D, ha demostrado su capacidad innovadora en los sectores de automoción, automoción, aeroespacial, UAS y en todos los sectores avanzados.
Su capacidad para reducir los tiempos de ciclo del producto (acelerando el tiempo de lanzamiento al mercado), ha dado a sus clientes una ventaja en el rendimiento del producto que aún no ha sido desafiada.
Comments